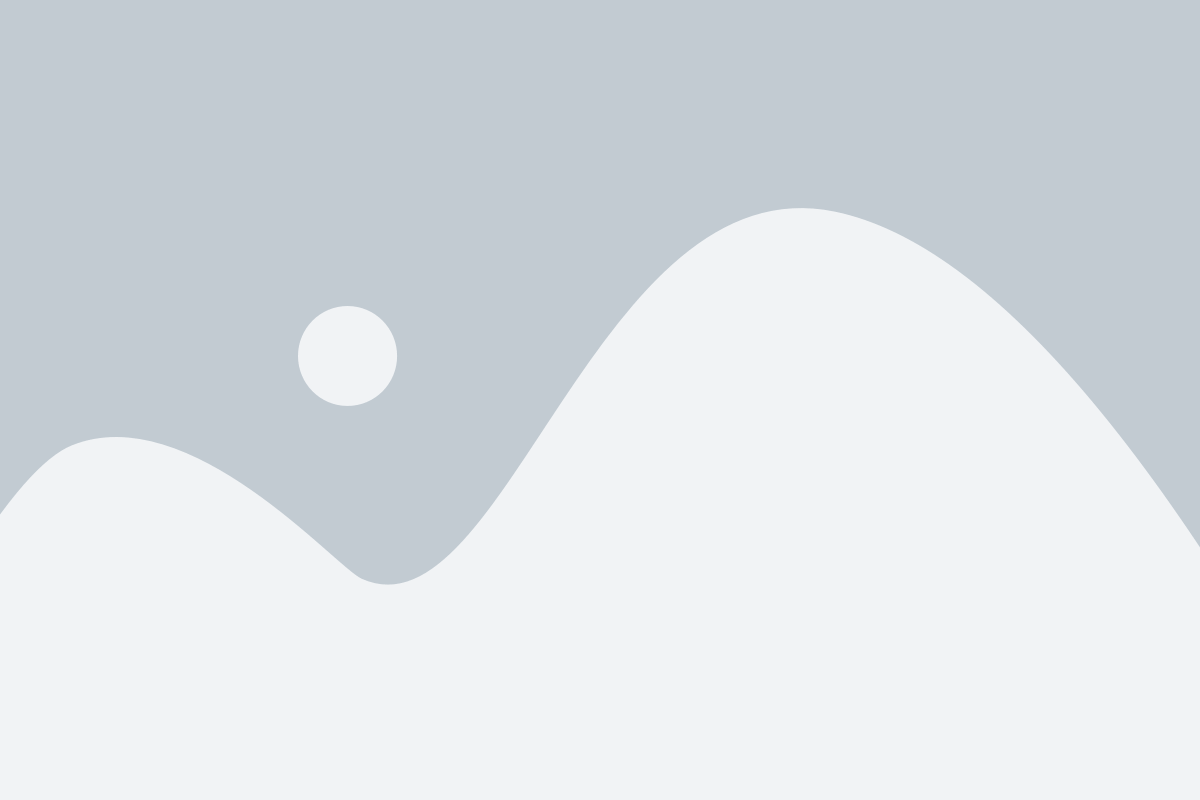
Our growing range of accessories complements our pumps to give you accurate control and monitoring capability.
Easily control your chemical injection pump, locally or remotely with the SIAT75001.
Our most sophisticated controller, the SIAT72000 can remotely monitor and control up to 4 pumps at the same time.
Highly accurate flow monitoring and pump leak detection of up to 4 pumps. Monitor and alarm up to 4 tank levels. SCADA with control available worldwide via cellular or internet networks. Extensive data logging capabilities.
Monitoring pump strokes provides an indicator, on its own or in conjunction with other metrics, that the pump is working optimally.
The digital output stroke counter senses the rotation of the pump’s crankshaft (cycle) to count the number of strokes. It does this without coming into contact with any of the pump’s moving parts by way of a proximity sensor. The senor emits an electromagnetic field, which allows it to look for a change in that field and return the signal. The output signal can be read by SiA’s pump controllers, a PLC, or other device.
Protecting against debris like dust, dirt and sand to improve the life of the motor and chemical injection pump in harsher conditions.
The SIALD9000 detects the presence of liquid (the leak) and provides a digital output, which can be read by SiA’s pump controllers, a PLC, or other device. Once the leak has been detected and attended to, the SIALD9000 can be dried and re-installed.
Leaks occur when the pump’s seals fail. Seal failures are caused by a number of issues including incorrect selection of seal material for the application; contamination; and normal seal wear.
Leaks can result in lower pump performance and if left unchecked, pump failure and ultimately pump damage and unit downtime.
A leak detector provides a warning of a pump leak, allowing operators to quickly remedy the issue before it damages the pump.
The sensor and associated electronics are housed within a capture vessel, which is connected to the chamber between the two seals of the SIA chemical injection pump such that any leakage past the high-pressure plunger seal is captured in the vessel that contains the sensor unit.
When no liquid is present (no leak) no output is received; but when liquid covers the sensor the output switches to indicate the presence of liquid (the leak).
The SIAFM80000 series utilise a positive displacement design to give a direct volumetric measurement of flow. The flow meters are not impacted by temperature, pressure, or viscosity variations.
The meter measures the individual output flow of each cycle of any SiA Chemical Injection Pump and converts this measured flow into an electronic output. This output can be displayed on an SiA controller.
These flow meters can also act as a “closed loop” flow control when used in conjunction with the SIAT72000 controller.
Hazardous area certified options are available.
A flow meter is a sensor that is used to determine the amount of fluid that moves through a piped system.
The flow meter has oval-shaped, geared rotors. Fluid differential pressure makes these intermeshing rotors rotate within the housing, catching a precise amount of fluid between the gear and the housing. The frequency of which provides a measurement of the volumetric flow rate.
Header Column #1 | Body Material | Fluid Ports ** | O’Ring Material* | Cable Entries | Temperature Limits | Pressure(psig) |
---|---|---|---|---|---|---|
SIAFM80001 | 316 SS | 1/8 npt female | Viton | M20 | 120° C | 1,500 |
SIAFM80002 | 316 SS | 1/8 npt female | Viton | 1/2” npt | 120° C | 1,500 |
SIAFM80003 | 316L SS | 1/8 npt female | Viton | M20 | 120° C | 5,580 |
SIAFM80004 | 316L SS | 1/8 npt female | Viton | 1/2” npt | 120° C | 5,580 |
* Other elastomers available upon request
** 1/4” ports available special order Viton
Pump setting gauges provide an efficient way to check the pump’s actual flow rate in the field. They also give a visual indication of tank levels. We use KENCO pump setting gauges, which are trusted around the world for their quality design and manufacture.
Injection rate calibrations can be made by isolating the gauge from the supply tank and then measuring the start level and finish level on the gauge when the pump is running for a set period of time (or set number of strokes). This injection rate of the pump can then be adjusted accordingly